With the decline in the birth rate and the aging of the population, ensuring labor and technical capacity has become a problem for the entire manufacturing industry.
In particular, the transfer of skills from skilled workers is an urgent problem that affects productivity and quality.
In this case, Omron launched a project to convert the “crafts” grown by artisans in its mold making department into the Internet of Things.
We interviewed the members who participated in the project, which can be called manufacturing innovation.
Use digital technology to transform your personality in manufacturing
Omron has made various efforts to improve production efficiency through the use of digital technology, such as computer development, design automation and the use of 3D data.
This time, the “Mold Making Internet of Things Project” was launched at the Omron plant in Kusatsu.
“Today’s manufacturing industry faces several challenges, one of which is a lack of trained technicians. There are many obstacles to adopting technology to solve these challenges.
Therefore, first of all, we are shifting from the in-house manufacturing department to molds. I thought about this problem.. ”
This is what mold maker Kazunori Takagi said. The mold is made by a metal cutting machine called a machining center, but one of the members, Yuji Yamazaki, has cultivated the technology, experience, and intuition for many years to operate the machine.
The purpose of the project is to transform personal manufacturing that relies on skilled engineers into smart manufacturing using digital technology.
Perform resistance quantification in cooperation with automation center
Takagi recalled: “The most difficult thing is how to quantify the resistance to cutting when using a machining center.”
“Initially, we tried to quantify the shear resistance based on current changes during the cutting process, but could not detect small changes.
Therefore, we repeated tests with the automation center engineers (control systems engineers and control engineers). The development of the center was used.
The idea of the ‘predictive surveillance system’. Using the algorithm of the system to convert vibration data into sound opens the way, “continued Yamazaki.
In Yamazaki’s experience, “good” and “bad” of the cut state are defined from the sound obtained by converting the vibration data.
We work with the automation center to establish the best control conditions for each of the many tools and metal materials in the mold, so that the cutting speed can be optimized under “good conditions”.
Detection and control create new value
“Even if you call it a machining center, you can install countless tools on its tip. Since each product is unified, we incorrectly tried and got what kind of data.
However, our goal is not just Resistance value detection and quantification. After the resistance value is detected, the cutting speed of the machining center is controlled by a PLC (Programmable Controller) .
I believe that the project can be completed successfully by combining detection and control. About this project idea.
Finally, we visualize the machining resistance and successfully control the machining center speed by PLC based on the value.
As a result, machining time was reduced to 40% and tool wear was reduced to 20%, which exceeded expectations. I’ve been running for more than a year, including testing, but without problems.
Regardless of the skill of the worker, the best processing can always be achieved.
The efforts of members of the mold making department and members of the automation center have paid off, and Yamazaki’s “craft” is capitalized.
Co-create and connect to IoT-centric customer problem solving methods
“The Internet of Things is not just the purpose of collecting data.
Value can only be created by using and controlling data. This is an initiative that only Omron can do, because Omron has a number of PLCs and other control devices. I can say: “Takeshita continues
At times like this, the use of data from manufacturing sites using the Internet of Things has started to be rolled out to customers as a service called “i-BELT”.
“I-BELT” is a plan to work with customers to create an IoT-centric data collection, data analytics and innovative sites process to find the best value. Stay in touch with customers and keep innovating, not just once, this is important. ”
This “project to shape the Internet of Things” is just one example, but “i-BELT” has the potential to turn all field data that was not available until now into “a new value to protect production and quality. “. .
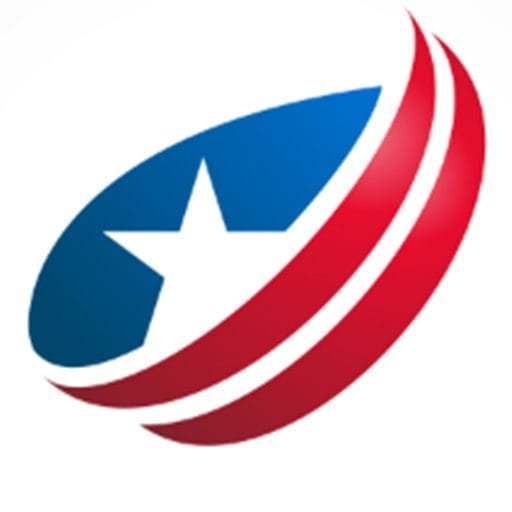
Odyssey has been the lead content writer and content marketer. He has vast experience in the field of writing. His SEO strategies help businesses to gain maximum traffic and success.